First 3D Printer for Drugs at UNC
First 3D Printer for Drugs at UNC
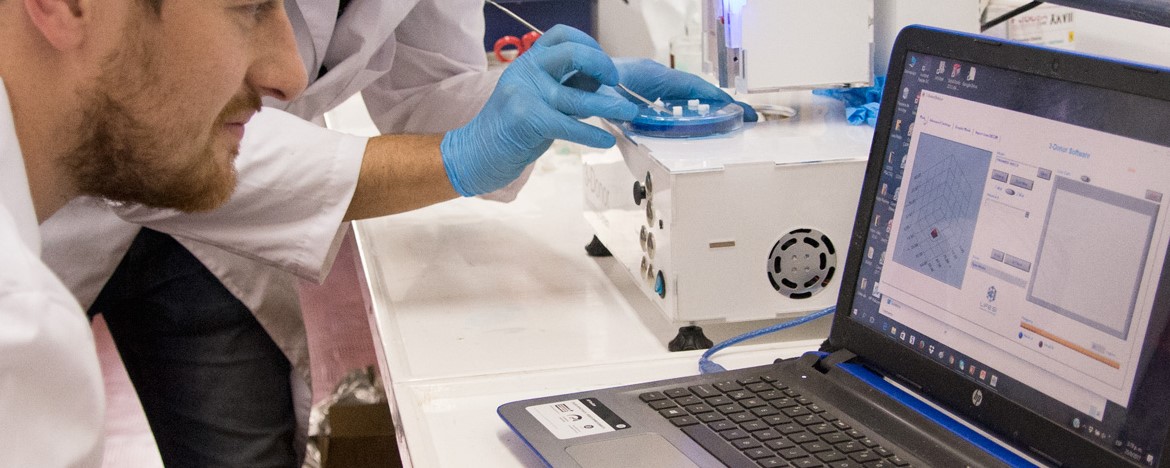
The printer has been pioneered in Argentina and is now operating at the UNC's Department of Chemical Sciences. It was developed by a national SME at the request of scientists from that department. By combining different materials, the machine can produce pills and capsules previously designed on the computer. The variety of geometrical shapes available enables for precise temporal and spatial control of drug release in the body. 3D printing promises to be very useful in the area of customized medicine, fabricating patient-tailored drugs. [04.16.2018]

3D printing allows for the manufacturing of objects you cannot even imagine. Nowadays, from houses to electronic chips to exact human organ replicas can be printed.
Eighteen months ago, the US Food and Drug Administration (FDA) has given the seal of approval for the production of the first-ever printed drug to treat epilepsy.
The use and development of that technology have arrived at the Department of Pharmacy of the Faculty of Chemical Sciences, National University of Córdoba. The printer is installed there and it can produce three-dimensional drugs, that is, drugs in real shape and form (physical, tangible objects) that are previously designed on computer.
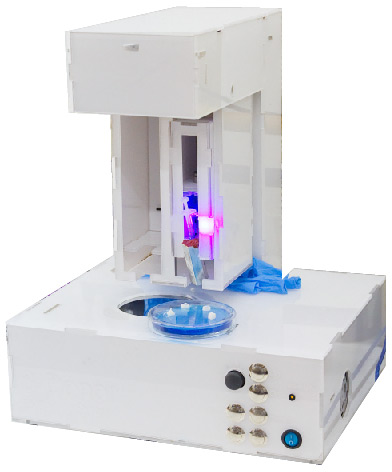
"The geometrical shape of the medication and the way in which its powder are combined (layered) influence directly on the release of the active ingredients," explains Santiago Palma, Ph.D. in Chemical Sciences and member of the UNC's group of scientists running the project. In this way, it is possible to have precise spatial and temporal control of the drug release in the body.
When printing drugs, two biocompatible materials are used: lipids or fats and water-soluble polymers, which are extensively used in the pharmaceutical industry. The active ingredients (drugs), responsible for the therapeutic effect, "are mixed" and "trapped" in the printed drug (See computer graphics).
Conventional drug production techniques involve the fusion of materials and the later solidification. These techniques are widely used in the production of many types of drugs (for example, suppositories), but one of the disadvantage is that they require molds, thus limiting the production to just one predetermined shape. On the contrary, 3D printing can customize medication in different shapes as the molding techniques are rid of. "We have tried with some active ingredients and have conducted many experiments on the release profiles with excellent results," says Palma, and clarifies that the project is now under the testing stage.
The 3D printer was designed and manufactured by a national SME (Life Soluciones Integrales), at the request of a UNC research group specialized in the field of pharmaceutical innovations. It functions with two specific computer programs developed by the company as well.
Until now, the scientists were able to print drugs in quantity, with compatible materials and with commonly used pharmaceutical industrial processes. It represents a "truly technological breakthrough," they assured. The challenge now is to accelerate the production process.
How does 3D printing for drugs work?
- The desired shape of the pill is designed using a computer program. It can be a cube, a pyramid or a cylinder. The shape is essential, as it is determinant in the rate at which the drug is dissolved in the patient's body.
The final result is a tridimensional image, whose coordinates are sent to the 3D printer. - The solid-state components (the active ingredient, the lipid and the water soluble polymer) are melted at the temperature of a little more than 50 °C.
The resulting blend is fed into disposable syringes, which are embedded in the 3D printer. - The syringe is placed in an electrical heating tube, so that the blend is kept in a liquid state and can flow easily during the printing.
In order to create the designed shape, the vertical chamber of the printer moves right and left. And the base plate where the syringe is embedded moves front and back. - A piston in the printer forces the plunger of the syringe so that the liquid-state blend is fed progressively.
The material is solidified at room temperature. The printing is carried out in layers so that the originally designed shape is created.
Customized medicines
Apart from being an innovative technological advance, the printer that is working at the UNC can have a great impact in the healthcare environment, benefiting patients who need a customized dosage according to their needs.
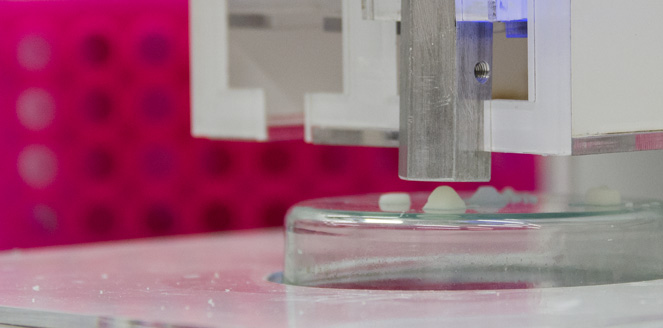
Nowadays, the customized production of drug is carried out in a "traditional" way in drug stores and in hospitals. Under medical prescription, the conventional drug dosage is adjusted to the patient needs and fit into common capsules (in the case of uncommon diseases and in pediatrics). In that sense, 3D printing could be a useful tool to produce in real time tailored-made drugs for each patient.
The ongoing project on which UNC researchers are working is contributing to a key area in the national scientific and technological development. In fact, 3D printing is part of what is called emerging technology and is considered a strategic issue within the framework of the Innovative Argentina 2020 Plan, dependent on the Ministry of Science, Technology and Productive Innovation, which establishes the guidelines regarding the country's science, technology and innovation for the next coming years.
- It allows for the combination of different shapes and the layering of materials, enabling for spatial and temporal control of drug release.
- The dosage of drugs is tailored to each patient needs.
- It employs a widely used technique in the drug industry (fusion and solidification), with the advantage that no mold is needed.
- No toxic materials are used. The lipid or fat (Galucire) is a slowly degradable substance and the polymer or plastic component (Poloxamer) is safe for human use and can be released rapidly in aqueous media (hydrophilic).
Team members: Santiago Palma, Juan Pablo Real, Alejandro Paredes, Nahuel Camacho, Marina Ardusso y Daniel Alemandi (Ph.D.s in Chemical Sciences). Department of Pharmacy of the Faculty of Chemical Sciences, UNC.
Funding: the project receives grants from the Science and Technology Secretary (Secyt - UNC), the National Scientific and Technical Research Council (Conicet) and the National Agency for Science and Technology Promotion.
Resources | Download full resolution images
Originally published at www.unciencia.unc.edu.ar on 08.24.2017
Translation: Lin Chun Wu